While our company works on all makes and models of aircraft, our focus in this edition is on the Cirrus SR20/22 lineup. Although we hope this may interest any aviation enthusiast.
As an authorized Cirrus Service Center, we specialize in avionics as well as maintenance for this airframe – and with an airplane as unique as the Cirrus, it’s worthy of its own distinction.

The Shake Up
The company began with a kit plane; approximately forty were produced in the mid-1990’s. The Klapmeier’s had a vision to a much larger scale. They pursued the Certified aircraft market, with the first SR20 receiving FAA approval for type certification in 1998. Since 2013, They have remained the largest producer of piston airplanes and the only manufacturer to include a complete airframe parachute on all models.
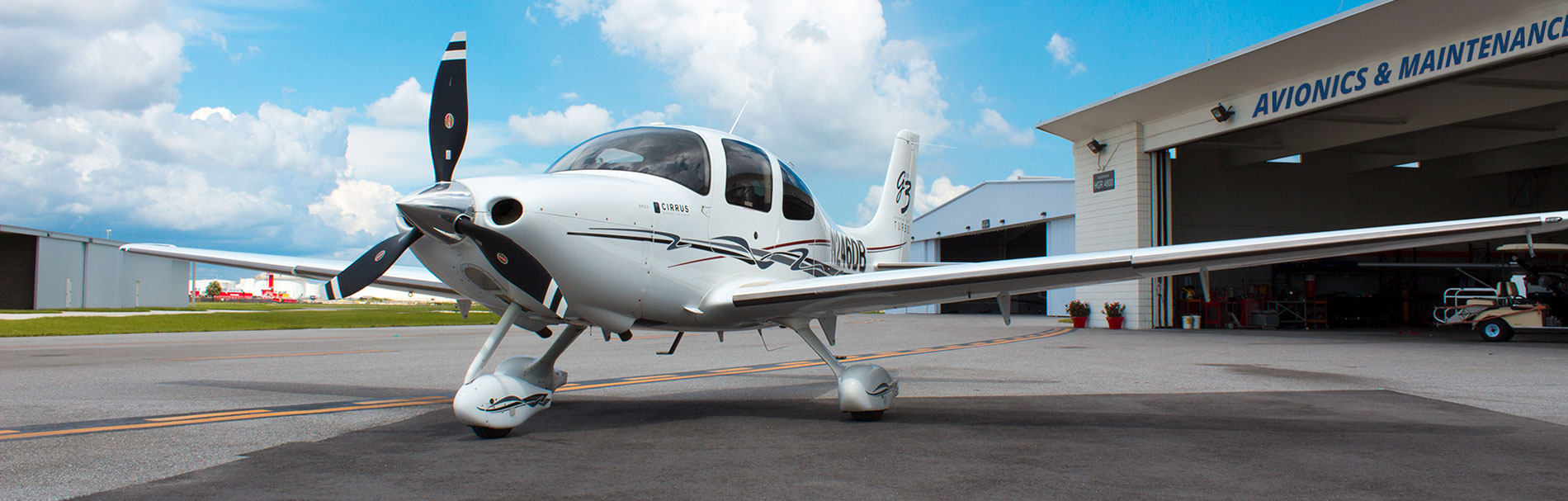
Hallmarks of the Pedigree
Cirrus ushered in a refreshingly new approach to the interior of the average general aviation airplane with automotive-like comfort. The side stick frees up cockpit space that is otherwise unusable or not visible, and passengers are therefore also more comfortable without the obstruction of a yoke. Furthermore, their foresight to shift the common steam-equipped GA cockpit to glass suites was an absolute game changer. In 2006, a revolution of digital avionics options arrived with the first all-glass equipped Cirrus, thriving alongside a new generation of Cirrus owners and pilots. And, let us not overlook and forget the loveliest of features that Florida pilots can appreciate: air conditioning.
Plenty has been written and said of the parachute being a design feature or marketing tool. Perhaps it is a bit of both: while chute deployment is a highly rare occurrence, it is an option for pilots presented with a worst-case scenario. Inarguably, there are circumstances in which there is no better option than to deploy the chute.
CAPS and Ownership
Consider this aspect of flying that many pilots oft become lax to: the preflight itself. That small task (= time) is an effort toward safety. Thus, with owning (and flying) a highly unique airframe comes its responsibility. The chute is a large reason why people purchase the Cirrus, and with that, in effect, comes a marriage to ownership, including the care and tenderness that every airplane deserves. With a Cirrus, the periodic maintenance and calendar or life-limited replacements of the Airframe Parachute System and rocket activation system will be needed to maintain airworthiness and must be completed by trained technicians at Cirrus Authorized Service Centers.
The System
The CAPS system consists of a parachute, a solid-propellant rocket to deploy the parachute, and a harness faired into the fuselage structure. A three-point harness includes two forward straps bonded to the fuselage, and the aft strap attached to the bulkhead located forward of the chute compartment.
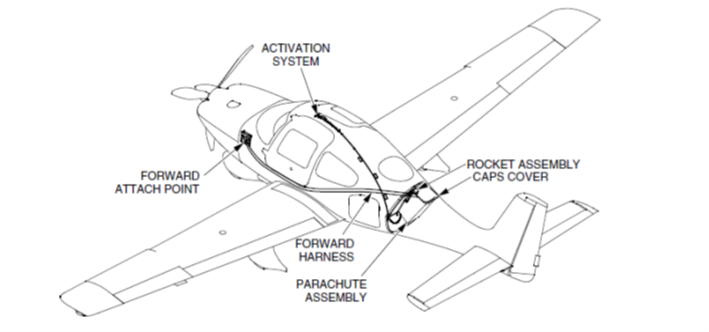
The parachute itself is a 2,400 square foot or 3,250 square foot (depending on model/serial number) round canopy designed with sliders along suspension lines. The slider is positioned at the top of the suspension lines and limits the initial diameter of the chute and the rate at which it deploys.
Two separate and deliberate pilot actions are required to deploy the parachute. The first action requires the pilot to remove the access cover from the activation handle enclosure. The second action requires the pilot to pull the activation handle out and then down several inches. The rocket impacts and disbonds the parachute compartment cover, pulling the deployment bag from the enclosure. The deployment bag then stages the suspension line deployment and inflation of the chute, pulling the aft harness taut, activating the line cutters, and eight seconds later, will “fire” and sever the nylon strap.
In eight seconds, forward velocity will reduce to zero and descent occurs at about 1700 fpm. The sequence aligns the aircraft in a touchdown attitude approximately ten degrees nose down, thus optimizing the safety of the passengers. As of the time of this writing, 253 people credit successful CAPS deployments with their lives. SOURCE
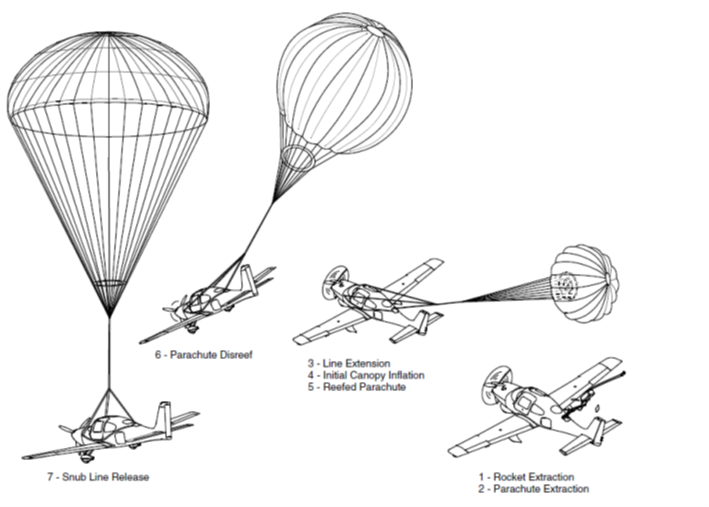
Maintaining Your Cirrus
The propellant-powered rocket requires specialized work and certificated training governed by the Bureau of Alcohol, Tobacco, Firearms and Explosives. Our technicians must also receive specialized training at Cirrus – not just any shop or A&P/IA can perform this service.
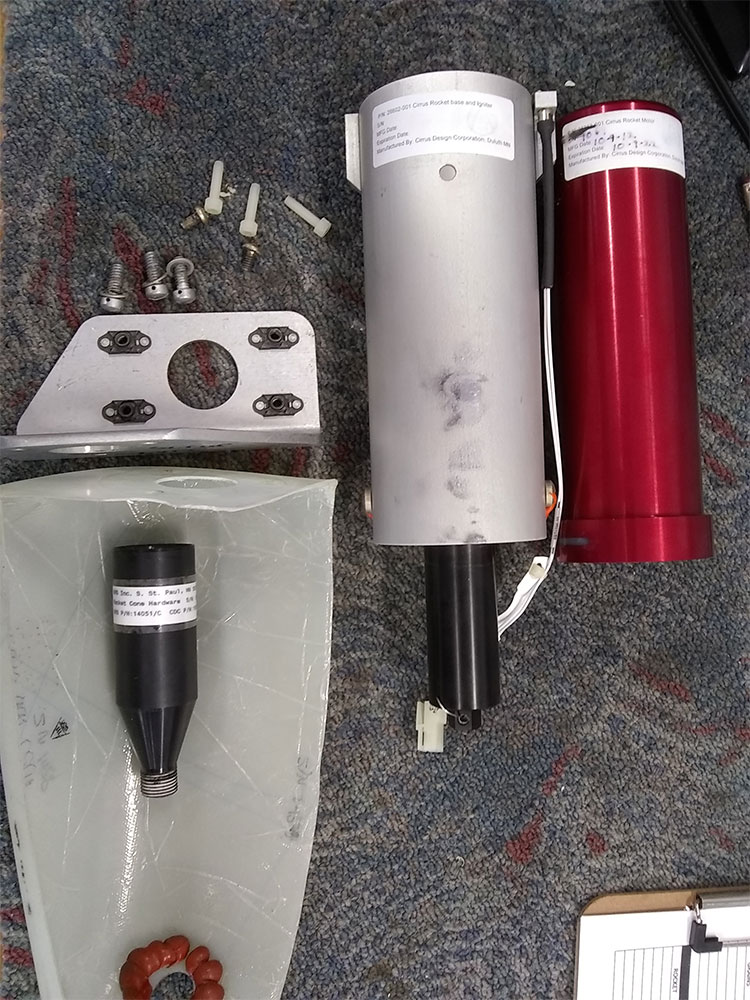
Generation One
The prerequisite for a G1 CAPS repack includes a bonding repair to the composite structure. In this process, the CAPS access cover is removed by drilling a hole into the fiberglass cover and using a slide hammer to break the bond between the fuselage and the cover plate.
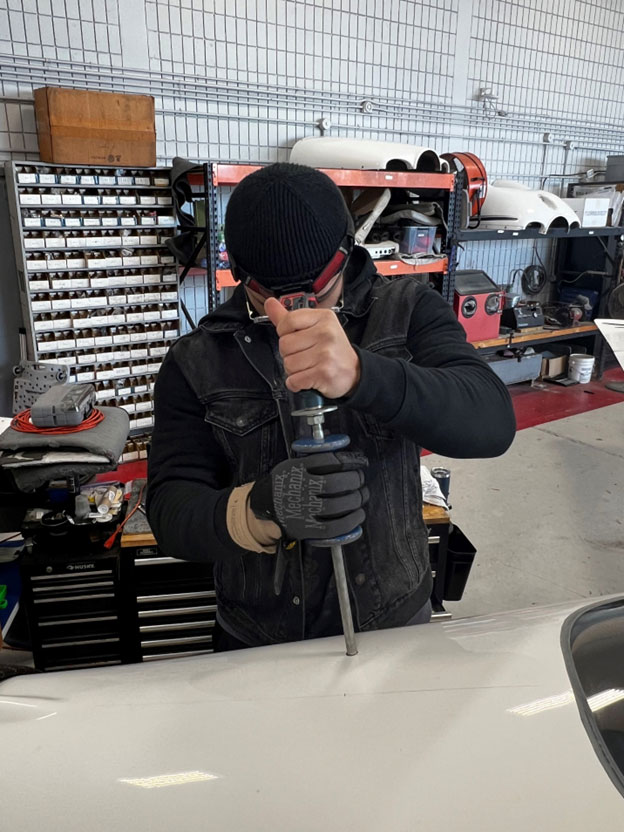
Removal of the empennage cover allows the technician access to remove the parachute after disconnecting and removing the rocket, the reefing line cutters, and the three straps, through the 222-bulkhead access panel in the baggage compartment. This step often requires a little finesse and muscle in perfect ratio, as we are dealing with both rockets and composite structures.
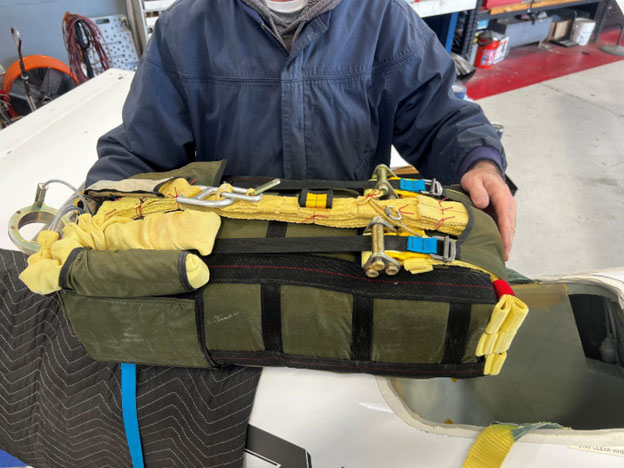
The old #2 battery enclosure and wire harness is then removed. A new enclosure is installed, along with a new wire harness, required to activate the new upgraded electric rocket ignition system. Note: Few and uncommon, some early Cirrus models were factory equipped with only one battery. A Service Bulletin calls for adding a second battery in addition to the repack. Those not equipped with a #2 battery thus require the installation of an additional battery for the electric ignition which includes the routing of additional wiring. At the time of this writing, given the service life of the chute, it should have already been replaced. If you’re in the market for an airplane, a pre-buy inspection should help ensure that requirements are met and airworthiness maintained.
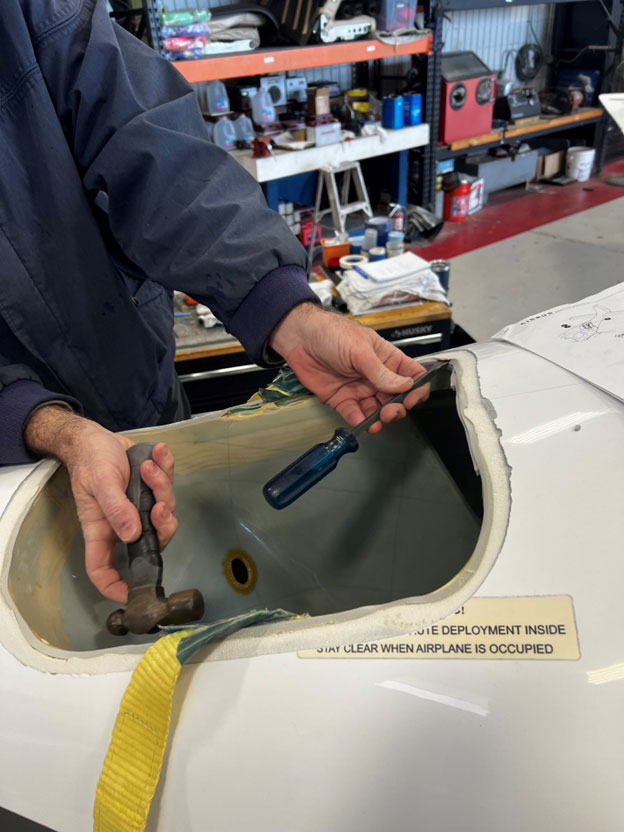
Once the new parachute, hardware and rocket are fitted into the bay, the new cover will be bonded into place. The new cover is cut, trimmed, and structurally bonded into place. Body filler is then applied, sanded, sealed, primed and painted to match. This is a meticulous process, requiring application of specialized Cirrus composite formulas, sanding and paint matching.
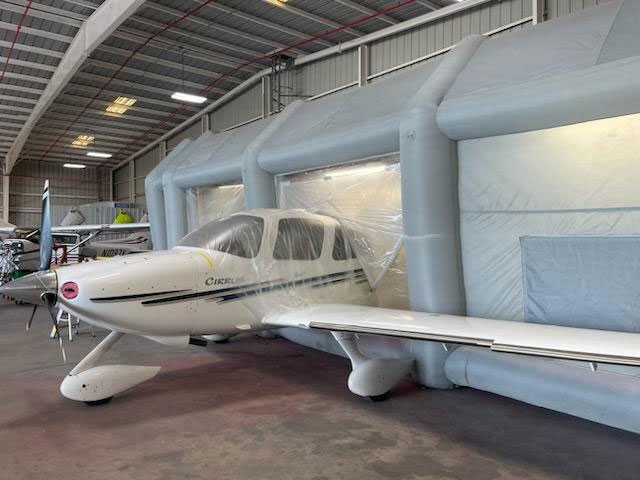
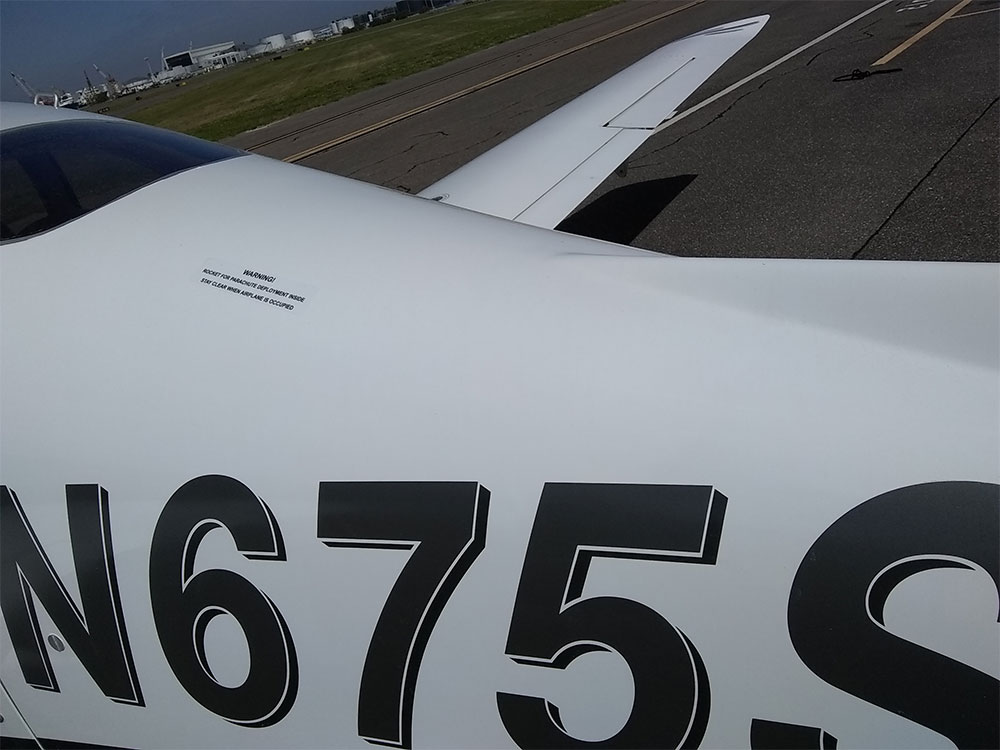
A Perfect Finish: matching the ten-year-old white paint is one of our specialties, as you can see.
Generation 2 and Beyond
The Generation 2, introduced in early 2004, brought about a new fuselage design, granting access to the CAPS compartment through the baggage bulkhead, eliminating this crucial process that is required on the G1 CAPS repacks.
CAPS maintenance and replacement on later models is like the Gen 1, but without removal of the empennage caps cover. The chute is removed through a larger 222-bulkhead access located in the baggage compartment. All aircraft not equipped with the new upgraded electric rocket ignition system will be required to comply with the applicable Service Bulletin modifications for the upgrade. If this has already been completed, we then only replace the chute and the rocket.
In 2013, Cirrus introduced the G5 SR22 model, which featured an increase of 200 pounds in useful load. After years of design and testing of a larger canopy, the CAPS system incorporated a larger, more powerful rocket with electronic versus percussion ignition, allowing the system to handle 3,600 pounds.
Every step of this meticulous process can be considered major surgery, and thus critical for a safe chute deployment. Every line, pin or component has been designed for optimal chute operation, so each step has its own technique, down to the position of the straps after chute removal, the details of the suspension lines and general inspection of the system. Our Cirrus Team Manager, Minh Ngyuen, and his team have received the required CAPS Certified training at the factory in Duluth, MN. We don’t sacrifice speed for safety, as your life depends on our quality service.
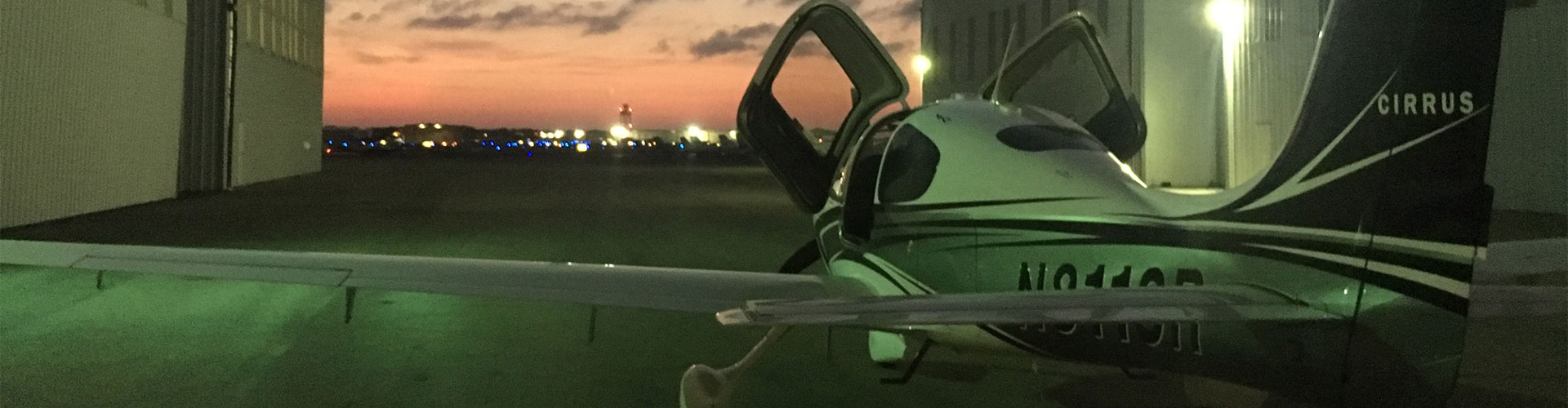
Perspective
To the non-flying community, this airplane is a no-brainer. While nervous passengers may cast a side eye toward general aviation aircraft, they may consider boarding the parachute-equipped Cirrus. Perhaps this was the vision of co-founder Alan Klapmeier, who personally survived a midair collision, and thus envisioned a life-saving device for all of the general aviation community. Which means more flying for everyone – and isn’t that a silver lining?
About Our Company
Our staff consists of people who got into this business because they love aviation. We are always here to answer any questions you may have about all of the current avionics options, and to help you find the right solution for your aircraft.
Besides offering the best prices and customer service in the industry, Sarasota Avionics & Maintenance sets itself apart from the competition by offering multiple locations throughout Florida. Providing both avionics and maintenance services all under one roof makes scheduling easier with far less downtime.